RELY ON AN INTEGRATED 3PL TO ORCHESTRATE YOUR COLD CHAIN
How strategic alignment across refrigerated drayage, warehouse distribution, and transportation protects your brand and your bottom line
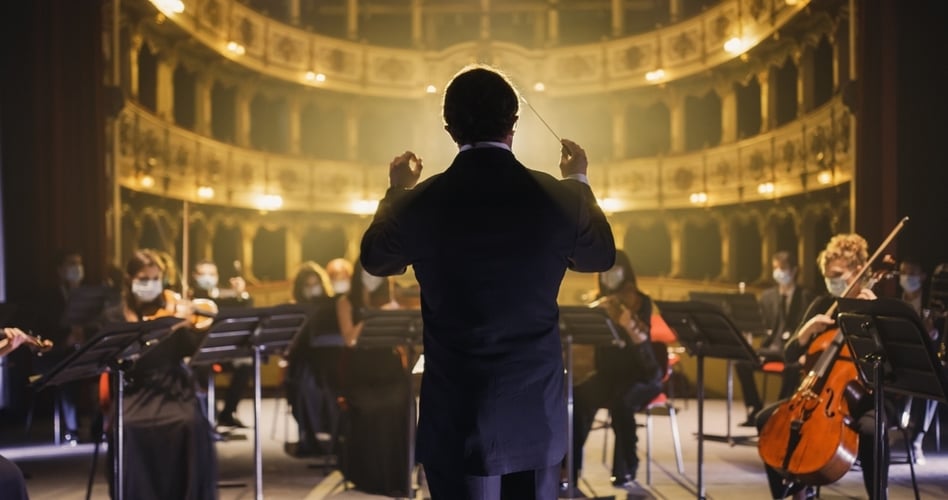
Refrigerated freight doesn’t move itself. It takes people, systems, and tightly coordinated processes to keep food and confectionery products safe, compliant, and on schedule. Yet in today’s logistics landscape, it’s still common for companies to rely on a patchwork of providers: one for drayage, another for LTL, a third for storage or cross docking. The result? Gaps in communication, misaligned standards, and increased risk of temperature fluctuations, delivery failures, and customer dissatisfaction.
A smooth-running cold chain is not just about moving freight—it’s about orchestrating it. That means working with a 3PL that doesn’t just offer refrigerated services but integrates them across the entire journey—from port to warehouse to store shelf.
This eBook outlines the key capabilities of a refrigerated trucking 3PL that can integrate all major legs of the cold chain—drayage, transportation and warehouse distribution. Such a provider can speed distribution, simplify vendor management, and offer greater protection for your food and confectionery products.
Download this article as a PDF
Fragmentation and the Margin for Error
Cold chain logistics is far more complex than standard freight movement. And when each leg of the journey is handled by a different provider, the margin for error increases.
1. MORE HANDOFFS = |
2. INCONSISTENT SOPs | 3. LIMITED END-TO-END VISIBILITY |
4. DELAYED PROBLEM RESOLUTION |
Each provider transition introduces a new opportunity for:
|
Not all providers follow the same protocols for trailer pre-cooling, product staging, temperature set points, or tracking. Lack of standardization leads to uneven performance—and increased spoilage or compliance risks. |
Without a unified system, it becomes difficult to track temperature logs, shipment status, and custody chain across providers. This makes it harder to respond quickly when something goes wrong—and harder to prove compliance during audits. |
When something does go wrong (a reefer fails, a delivery is delayed), it’s not always clear who’s accountable. This slows down response times and increases the likelihood of product loss or customer dissatisfaction. |
The Integrated Cold Chain Provider Removes These Concerns
Integrated logistics services mean having large swaths of your supply chain—drayage, warehousing (including cross docking and transloading), FTL, LTL, pool distribution, freight consolidation—managed by a single provider.
The benefits of this integration are clear: fewer handoffs, tighter scheduling, more consistent temperature control, and unified communication. When your freight doesn’t need to change systems or switch between third parties at each step, the risk of service failures and temperature excursions drops dramatically.
For example, when a refrigerated 3PL can manage port pickup, cross dock at its own temperature-controlled facility, consolidate LTL shipments bound for a specific region, and deliver to multiple retailers—all within the same network—the result is higher performance and lower costs.
Integrated Cold Chain Services in Action
Prelude: Unique West Coast Port Challenges
The opening movement in this orchestra piece begins at the port. But the complexities of refrigerated port drayage are frequently underestimated. Managing appointments, ensuring reefers remain powered while waiting in congested yards, and coordinating swift handoffs from ocean to inland transportation are all critical tasks—and any misstep can lead to costly temperature deviations, detention charges, or even spoiled product.
These complexities are magnified at the major California ports of Los Angeles, Long Beach, and Oakland. The Golden State introduces its own unique set of operational challenges that many national 3PLs are simply not equipped to navigate. These include congestion, environmental regulations, and labor laws. California’s Assembly Bill 5 (AB5), for example, has dramatically reshaped the trucking landscape by limiting the use of independent owner-operators. As a result, non-compliant or unprepared carriers may suddenly face capacity shortages or hefty fines—jeopardizing your freight and your wallet in the process.
Port-specific expertise is no longer optional for temperature-sensitive cargo entering California. A qualified 3PL must understand not only the physical logistics of working in and around marine terminals, but also the regulatory frameworks governing access, equipment, and labor. This includes navigating California’s strict emissions requirements (such as CARB rules on reefer units), chassis availability issues, and compliance with union labor practices at the ports.
An integrated 3PL with its own reefer drayage capacity and regulatory experience ensures your cargo moves efficiently from ship to shore, stays powered, and avoids detention—even in one of the most complex logistics environments in the country.
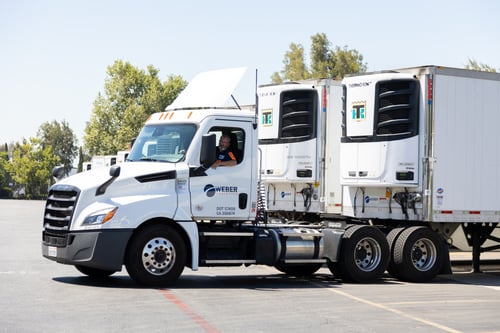
Asset-based vs Non-Asset for Cold Chain Logistics
As logistics strategies evolve, many providers market themselves as “non-asset-based” to highlight flexibility. But in the cold chain, having direct control over equipment (e.g., tractors, trailers, reefer units, chassis), and drivers remains a significant advantage—especially when it comes to service reliability and capacity.
An asset-based 3PL owns its fleet and employs its drivers, meaning it can make firm service commitments, set its own maintenance standards, and maintain a high level of temperature-control compliance. In times of market disruption, asset-based providers are less reliant on the volatile spot market and can often shield clients from capacity crunches and rate spikes.
That said, non-asset capabilities offer essential scalability. Some 3PLs offer a hybrid model—where a 3PL owns enough equipment to secure consistent performance on high-priority lanes, but also has vetted broker partnerships to flex up or down based on seasonal or geographic needs.
When evaluating a refrigerated 3PL, ask how they balance owned assets with brokered solutions, and how they maintain service quality across both.
Movement II: The Warehouse
The warehouse is where the cold chain either stays intact—or breaks down. It’s more than a stop on the journey; it’s the operational bridge between import arrival, inventory strategy, and final-mile delivery. When your drayage provider can also integrate cold storage, cross docking, transloading, and order fulfillment into their transportation operations, you enjoy greater consistency, flexibility, and risk management.
Transloading plays a critical role—especially for imports arriving at ports. Transloading refrigerated containers into domestic trailers at temperature-controlled facilities allows shippers to avoid port chassis shortages, reduce dwell time, and streamline inland transportation. This is particularly valuable in California, where port congestion and regulatory complexities can slow container movement. A provider that can quickly and safely transload product at or near the port ensures minimal disruption and maximum freshness.
Just as important as transloading is the strategic placement of refrigerated warehouse capacity. A network of temperature-controlled facilities within a concentrated logistics hub—such as California’s Inland Empire—offers shippers the ability to position freight closer to high-volume consumer markets while maintaining flexibility. This geographic density supports dynamic inventory strategies, like zone skipping, just-in-time fulfillment, and faster replenishment for retail or foodservice accounts.
In this kind of network, product arriving at a port can be received at a cross-dock, staged for short-term storage, or consolidated into outbound loads for retail DCs and major grocery chains—all within a tightly managed, refrigerated ecosystem.
Warehouses that follow food-grade SOPs, maintain dedicated refrigeration zones, and support multi-temp strategies ensure that cargo stays in compliance while moving efficiently. In a well-orchestrated cold chain, warehousing isn’t just a passive waypoint—it’s a central hub for freshness, efficiency, and service excellence.
Case Study: Integration in Action
Weber Logistics Performs Integrated Reefer Transport for a Legendary Chocolate Brand
A beloved chocolate brand needed a flexible, temperature-controlled transportation partner to support a wide range of services—from full truckload to pool distribution—while navigating complex final-mile deliveries to unique locations like Disneyland and the Las Vegas Strip.
Solution:
An integrated, asset-based 3PL provided the chocolatier with:
- FTL, LTL, stop-offs, and pool distribution
- Drop trailer service at the brand’s California DC
- Company drivers trained for both retail DCs and hard-to-reach urban destinations
Impact:
Consistent refrigerated service across CA, WA, NV, AZ, and OR—moving over 750,000 lbs/month of premium confectionery products.
Movement III: Out for Delivery
Once cargo is staged, consolidated, or cross-docked at a temperature-controlled warehouse, it must be distributed to its final destination: retail DCs, grocery chains, foodservice customers, or direct-to-consumer hubs. The final phase of the cold chain may involve one or more of the following refrigerated transportation modes:
- Full Truckload (FTL)
Best suited for high-volume shipments or long-haul moves where a full trailer is needed. Offers tighter control over scheduling and temperature since freight is not shared with other customers. - Less-Than-Truckload (LTL)
Ideal for smaller palletized shipments that don’t require an entire trailer. However, LTL adds complexity, as cargo may be handled multiple times and travel through terminal networks. Integration here ensures minimal exposure and faster transit. - Pool Distribution
A cost-efficient method where goods from multiple shippers are consolidated into one truckload and then delivered in regional “pools” based on geography. Especially useful for retailers or grocers with tight delivery windows and/or multiple store locations. - Freight Consolidation
Similar to pool distribution but focused more on aggregating multiple small shipments into a single truckload to reduce costs and improve efficiency.
When managed by separate providers, these services can become disjointed. But when a single integrated 3PL manages all modes under one operational umbrella, the result is harmonized scheduling, tighter temperature control, and clear communication across the entire route.
What to Look for in Your Integrated 3PL Provider
Safety First
When looking for the right logistics provider for your food or confectionery cold chain, the first order of business is making sure that the provider can maintain the integrity of your products.
For temperature-sensitive products, a few degrees might spell the difference between a trip to the market and a trip to the landfill. 3PLs who handle food and confectionery logistics will deploy temperature-monitoring technology to monitor the environment through all phases of the supply chain – in the warehouse, on the dock and over the road. This information allows 3PLs to react quickly, if necessary, to bring the temperature back to spec.
Importantly, the proactive management of temperature integrity is no longer just sound business practice, it’s the law. The Food Safety Modernization Act (FSMA) focuses on the prevention of foodborne illness and holds shippers largely responsible for defining what constitutes safe practices for food handling and transportation.
These practices must be clearly defined in a Food Safety Plan. Adherence to this Plan – and the temperature requirements within (if applicable) – is an important responsibility of all members of the food supply chain.
Trusted external agencies such as AIB International perform audits of 3PL operations to ensure compliance with such regulations and award superior ratings to only those who fit the bill. If your prospective provider regularly undergoes such external audits, that’s a good sign that it ‘walks the walk’ when it comes to food safety.
Additional ways to see if your provider is buttoned up when it comes to temperature-controlled product safety include:
- Ask how reefer trailers are monitored during temperature-controlled transport. At the very least, they should carry digital thermostats that are easily visible to the driver. At best, data is transmitted via real-time connectivity, allowing dispatch managers to assure complete control.
- Ask about backup plans. If the cooling or system goes down, how will the company maintain the right temperature until it’s repaired?
- Ask to see logs that show temperature readings over time.
- If the LTL provider also performs warehousing, take a tour of its facility. Temperature monitors should be visible in all locations, with separate units at the top and bottom of multi-level racking, and digitized records proving the integrity of temperature control the storage environment.
Additional considerations in finding the right provider
- Compliance Isn’t a Perk—It’s a Baseline
Regulatory frameworks like the FSMA, FDA, and GFSI demand rigorous cold chain control. Certified providers demonstrate their readiness not just in the warehouse, but across drivers, dispatchers, and billing teams. Look for documented SOPs, third-party certifications, and compliance training that permeates the provider’s culture.
- Temperature Control Is More Than Equipment—It’s Accountability
Real-time temperature monitoring should be supported by clear escalation procedures, empowered staff, and continuous monitoring across every handoff—from trailer to dock to final mile. Accountability means acting before an excursion becomes a problem.
- Trust Is a Team Sport: Service, Safety, and People
Look for experienced CSRs, safety-minded drivers, and cross-functional teams that communicate seamlessly. Tenure, training, and alignment across customer service, billing, and operations are signs of a strong provider culture.
- Tech That Doesn’t Just Track—It Transforms
The best cold chain tech provides more than visibility—it delivers insight. Look for dashboards that show performance, automate compliance reporting, and integrate with your existing platforms. Bonus points for predictive analytics and exception management tools.
Checklist: Is Your 3PL Orchestrating Your Cold Chain—or Just Moving Freight?
Dedicated reefer drayage from major West Coast ports
Seamless integration of LTL, FTL, pool distribution, and consolidation
Real-time temperature tracking and alert escalation
AIB- and FDA-compliant warehousing with documented SOPs
Hybrid model with both asset-based and brokered capacity
Long-tenured CSRs, drivers, and warehouse staff with specialized training
Tech platforms that offer full-chain visibility and actionable insights
Cold chain-compatible warehousing with cross-dock and staging services
If you’re not checking most of these boxes, it may be time to rethink your cold chain strategy—and look for a partner who can bring it all together.
Final Word: Orchestrate with Confidence
The cold chain has too many moving parts to manage in silos. The best-performing shippers work with logistics partners who think beyond the trailer—those who integrate systems, align teams, and build infrastructure to support the full refrigerated journey.
Whether you’re moving confectionery through LTL lanes, managing reefer drayage at the port, or staging pharma products for final-mile delivery, the right 3PL doesn’t just help you execute—they help you orchestrate.
Want to Learn More About Our Agile 3PL Services from the West Coast?
Call 855-GO-WEBER or email
sales@weberlogistics.com
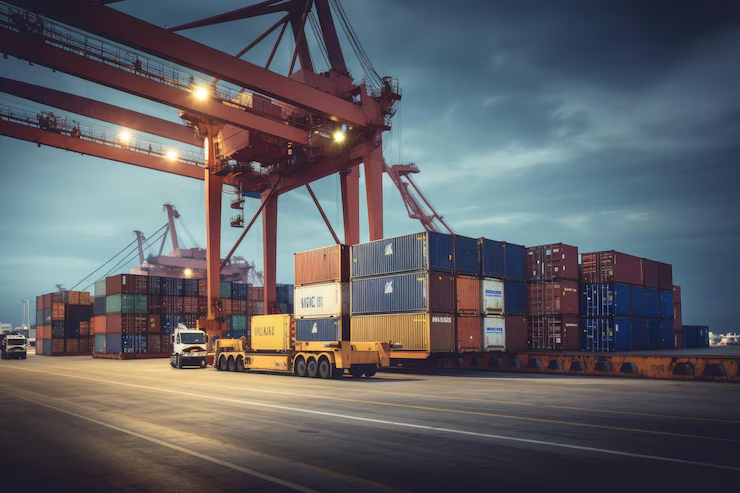