Candy products come in all shapes, sizes and colors, but share many of the same needs from a logistics standpoint. They all need to be carefully handled throughout the supply chain so that they reach customers exactly as intended. In this article, we’ll examine the cold chain logistics services a third-party logistics provider (3PL) can provide to protect the integrity of your products every step of the way.
But first…food safety certification
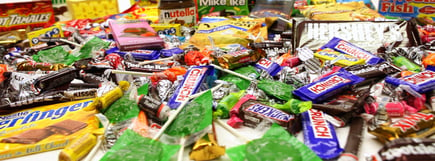
Before you get too familiar with a prospective 3PL’s service offerings, it’s important to make sure it has the proper certifications to handle your products. You’ll first need to ensure that the 3PL’s warehouse is registered as a food-grade facility with the FDA.
From there, you’ll want to know that the provider is in compliance with all modern food safety requirements, including those set by the Food Safety Modernization Act (FSMA) and the Global Food Safety Initiative (GFSI). Trusted external agencies such as AIB International perform audits of 3PL operations to ensure compliance with such regulations and award superior ratings to only those who fit the bill.
Depending on the nature of your operation, there is other documentation you may want to see. If your products are organic, for instance, you’ll want to know that your provider has organic certification from a reputable agency such as Oregon Tilth.
Cold chain logistics services for the confectionery industry
Your 3PL partner can provide the following services for your candy products.
1. Temperature-controlled container drayage. If your products are coming into the U.S. from overseas, you will need a 3PL to perform port services such as drayage (receiving your containers and transporting them to a distribution center) and/or transloading (receiving your containers, transporting them to a DC, stripping the container, and getting products out to their final destinations quickly).
You’ll need to ensure that your provider can meet your products’ temperature requirements throughout these crucial supply chain steps. For refrigerated containers, you may need a carrier that has the experience to handle 'gensets,' including the potential need for either charging stations or electric hook-ups. For transloading, you’ll also need to ensure that the 3PL can prepare outbound loads in accordance with the vendor compliance guidelines of your retail partners. Finally, if you’re shipping into California ports, you’ll probably want your provider’s drivers to be hourly employees and not independent contractors due to the ongoing battle over driver classification in the state.
2. Temperature-controlled warehousing. Your 3PL’s warehouse will be ‘home’ for your products as they await final distribution. And, like any home, you’ll want it to be comfortable and have modern amenities including the following.
- Temperature control. Your products have specific storage conditions that must be met in order for their integrity to be preserved. It is the responsibility of your 3PL to make sure that these conditions (e.g., keeping products between a set temperature range) are in place and monitored 24/7. Equipment should be regularly inspected and maintained, and an alarm system – and associated protocols – should be in place should conditions ever fall out of range.
- A robust warehouse management system (WMS). The modern warehouse offers a lot more than simple storage. Your 3PL’s WMS system acts as the operational hub of the building, handling everything from lot control and inventory management (e.g., FIFO) to real-time order tracking and KPI reporting.
- Recall capabilities. In the event of a recall, you’ll need to know that your 3PL provider has the systems and planning in place to handle it effectively. It all begins with the WMS and its ability to quickly identify product lots within inventory, place a hold on the lots in question so that they cannot be shipped, and segregate the lots away from the general product population.
Importantly, your 3PL should be able to track the whereabouts of your product in real-time, while providing you with visibility you need. The 3PL should also be able to track the temperature of the trailer in real time, so that if there ever is an issue with the consignee, you will have documented temperature readouts of your product throughout its journey.
4. Pool distribution. Another transportation-related cold chain logistics service is pool distribution. This cost-saving service is an effective alternative to higher-cost, national LTL shipping.
With the LTL model, companies that don’t have the volumes to ship full truckloads have to rely on temp-controlled LTL carriers. There aren’t many of these carriers, though the demand for them is consistently high. Because of this, you will pay more for refrigerated LTL compared to other modes of transport. Additionally, LTL shipments can take as long as nine days to move long distances through the LTL terminal network, resulting in extra time on the road and extra touches of your product.
The pool distribution model, on the other hand, allows your products to share the ride (resulting in reduced costs) with other products heading to the same destination (e.g., retailer DCs). With this model, you ship your palletized products to one distribution point – typically the warehouse of a 3PL that offers temperature-controlled pool distribution. The 3PL breaks down your products and prepares them for final delivery. It also does the same for other companies’ products that have the same temperature needs and are headed to the same destinations. The 3PL then combines your products with those of the other companies, combines them into full truckload shipments, and performs the final deliveries.
Lean on a 3PL for cold chain logistics services
Whether you need drayage, warehousing, or transportation services for your candy products, there are 3PLs that are up to the task. Some 3PLs, like Weber Logistics, handle all of these services – providing a fully integrated approach to your cold chain. With asset-based trucks and equipment and all the ratings and certifications you want your 3PL to have (including AIB and Oregon Tilth), Weber is a trusted West Coast logistics partner for many of the candy world’s most iconic brands. To learn more about Weber Logistics’ services, contact us today.