For large-volume importers, drayage costs and port fees can eat up a good chunk of the transportation budget. So it pays to dig in and understand where the money is being spent and whether smarter, cheaper alternatives exist.
The following are a few tips to reduce drayage costs and port fees on the West Coast.
Port drayage: when faster isn’t necessarily better
Most importers want dray carriers to pick up containers on the first day they become available. But, depending on labor capacity at the warehouse, that may not be the best idea. If a large number of containers are being pulled, they may end up sitting in the warehouse yard until the warehouse operator – either you or your 3PL partner – marshals the labor to complete the unloading.
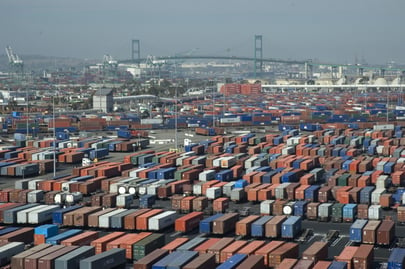
When containers sit, chassis fees may apply and you’ll pay $32.50/day for every day the chassis is out. As for containers, shipping lines typically allow 5 free days once the container is picked up. The fee for keeping a container beyond time is called a detention charge, which could be $100 – $200 daily, including weekends. So get those chassis and containers back before the port closes down for the weekend!
With the average dray move at $450, extra fees can be more than double the base delivery fee. It helps to work with a 3PL that combines drayage and warehouse services. When you do, the warehouse will dictate to their dray colleagues exactly when containers should be pulled to minimize wait time and related charges.
Are you really saving money by avoiding the PierPass port fee?
PierPASS was developed to relieve the Ports of LA/Long Beach from traffic congestion. The ports add an extra PierPASS fee of $167 per 40-foot container if your trucking partner (drayman) moves goods during peak hours between 8 am and 5 pm. For 2,000 containers, that fee adds $334,000 in costs.
Your carrier may charge you an extra $100 to pull at night to avoid PierPASS, but that still results in a $134,000 savings versus daytime pickup.
Worth it, right? Well, maybe.
Again, you need to consider all legs of the supply chain. If the receiving warehouse is closed at night, you’ll pay a “pre-pull” charge to bring the container to the drayman’s off-dock yard and deliver it at a later time. The cost of this “pre-pull” move can range between $75 and $125 per container, or $150,000 – $250,000 for 2,000 containers.
On top of that, you’ll pay the full delivery rate of $150–$200 the next day to bring it to the warehouse – an average of $350,000 for 2,000 containers. (We wrote more about this in an earlier blog on PierPass rates.)
Bottom line: if the warehouse is only open during the day from 6 am to 5 pm, you are better off ponying up the PierPass port fee. If the warehouse is open 24 hours or has a secure yard to drop trailers, you should use the port’s night gate and avoid PierPASS.
Can it be cheaper to pay higher drayage costs?
Absolutely. It comes down to the location of your warehouse relative to the Ports of LA/Long Beach.
With an Los Angeles warehouse, your transportation costs will be much less, but space and labor costs will be high and may offset your transport savings. Also, space can be tough to find in the congested LA basin.
In the Inland Empire, 60 miles or so east of LA, drayage costs will be 30% higher, but that is offset by real estate that is about 30% cheaper than LA. Labor costs are also lower here due to the cheaper cost of living.
A rule of thumb you can use to determine where to locate a Southern California warehouse is this: the quicker your products turn and the higher value they have, the closer you should be to the port. The slower your products turn and the more storage space your require, the further you should be from the port.
It’s best to get advice from a knowledgeable logistics partner, who can work through all the competing costs with you and help you decide.
Who pays the port fees?
Each port publishes fees for services such as dockage, demurrage, late charges, etc. You can pay port fees directly, or your 3PL partner can do it for you. If the 3PL pays, they may be adding a 15% upcharge to cover admin time.
It’s nice to outsource this administrative hassle, but at what cost?
That’s what you need to find out.
The best way to lower port fees and other charges
For thin-margin businesses, every dollar saved in logistics goes straight to the bottom line. But drayage costs and port fees are often not scrutinized as carefully as other freight and warehouses costs. For that reason, they can eat into profits unnecessarily.
Your best bet may be to meet with an integrated dray and warehousing provider that regularly serves the Ports of Long Beach and LA. Share your situation and ask for advice based on their experience. You may be surprised at just how much you can save.