In today’s fast-moving logistics marketplace, logistics technology plays a key role in determining how quickly, how accurately, and how correctly product can be delivered to the customer. But what kind of system, or systems, do you need? The major components are:
ERP (Enterprise Resource Planning) – This is the ‘Main Frame’ of old. This is the system where anything to do with your product is stored. Usually purchasing of raw goods through planning and building the finished goods, through handling customer orders and invoicing, flow through this system. It knows how much of what is where and in what stage of production it is in.
FMS (Finance Management System) – This system manages all your dollars, assets and liabilities. Sometimes this system is ‘built into’ the ERP system to help manage the costs of each step of your operation. Other times the ERP is interfaced to supply just the financial information to this system.
WMS (Warehouse Management System) – This system knows exactly how many and where every widget is within your warehouse(s). It can help drive better productivity by managing building layouts and travel time, and usually will direct your labor force via wireless devices vs. utilizing paper printouts. It is usually interfaced to your ERP in order to electronically communicate all receipts and shipments from the warehouse(s). There are MANY varieties of WMS systems, from generalized ‘do it all’ systems to specialized, one-purpose systems. It can be a daunting task to choose the logistics technology that fits your business, and your warehouse, the best.
TMS (Transportation Management System) – This is an often overlooked system as most businesses see this as a Carrier’s system vs. a system that can help save them money. All your goods have to get from your manufacturing site to the customer somehow, right? Having a good TMS that helps route and consolidate your shipments the quickest, most efficient, least expensive way can save you big dollars in the long run. This system needs to communicate to your ERP, FMS, and WMS systems to be the most efficient.
LMS (Labor Management System) – This is also an overlooked system as it deals primarily with productivity only. This system’s goal is to inform you of how efficiently your labor force is actually performing and help you plan future work more efficiently. Without some kind of LMS in place, how do you really know that all your employees are being as efficient as possible? How do you know how many people you need for the tasks planned to be completed tomorrow? This system should be tightly integrated with your ERP (for production work) and WMS.
Most companies have some sort of ERP and FMS systems already in place that work well for them. Some larger ERP systems have modules that try to handle WMS, FMS, or LMS tasks – but most have found these modules to be lacking the true, flexible functionality that specialized systems can provide. Where companies can save significant dollars is by investing in a true WMS, a TMS, and a LMS.
In a lot of cases manufacturers want to focus on manufacturing, not warehousing and shipping – hence they outsource these functions to Third Party Logistics providers who already operate efficient 3PL systems (e.g., WMS, TMS, LMS). The best 3PLs run all three systems as a tightly integrated logistics technology suite, increasing their accuracy and efficiency during every step of handling the logistics side of their customer’s business. Every penny saved by the 3PL not only transfers directly to their bottom line, it also transfers to their customers’ bottom lines with lower transactional rates, higher accuracy, less compliance chargebacks, and the ability to know exactly where every order, receipt, and widget is within the supply chain.
Logistics Technology Systems: A Primer
Similar Blog Posts
See All Blog Posts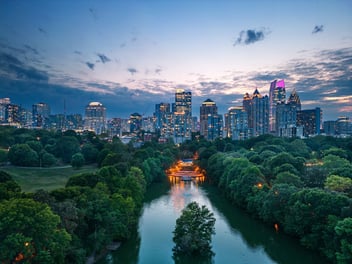
Atlanta logistics
August 21, 2025
The Advantages of Using Atlanta as a Logistics Hub
The state of Georgia consistently ranks at or near the top of ‘best states for business’ lists in publications like Area Development and Site Selection Magazine. It’s no surprise, then, that Weber...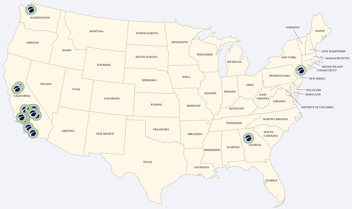
weber logistics news
August 18, 2025
Weber Logistics Goes National: Now Serving Atlanta, Seattle, and New Jersey
For over 100 years, Weber Logistics has been a trusted West Coast logistics partner, moving products seamlessly from port to shelf with precision, speed, and care. Now, we’re bringing that same...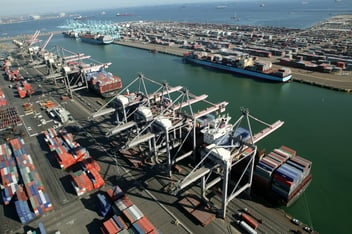
Southern California Ports
July 16, 2025
Happening Now: Port of Los Angeles Sees Record June
According to FreightWaves, the Port of Los Angeles had its busiest June on record, moving 892,340 TEUs—an 8% increase year-over-year. This is due, in large part, to retailers accelerating holiday...Subscribe to Instant Updates
Component variant main layer object list link mask create follower main vertical image blur comment bold variant opacity plugin italic.
