If done incorrectly, hazardous material storage of commercial inventory can be extremely dangerous. A single slip up or oversight doesn’t just impact line items on a balance sheet, it puts lives at risk. With the right provider, however, hazmat storage and distribution can be just as safe as the storage of any non-hazmat item.
To help you understand what the “right provider” might look like, let’s first ensure that we’re clear on the basics by answering some of the rudimentary – yet frequently asked – questions Weber’s chemical logistics specialists receive.
Hazmat Material Storage FAQs
What Constitutes a Hazardous Material?
According to the Institute of Hazardous Materials Management (IHMM), a hazardous material is “is any item or agent (biological, chemical, radiological, and/or physical), which has the potential to cause harm to humans, animals, or the environment, either by itself or through interaction with other factors.”
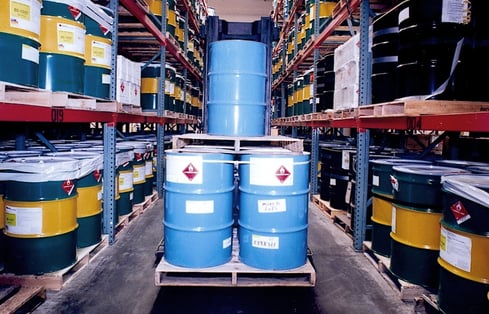
Such materials include chemicals and toxic substances and can be classified as physical hazards (e.g., flammable and corrosive chemicals) and/or health hazards (exposure to the material can cause acute or chronic health effects).
There are 9 different classes of hazardous materials that are further broken down into divisions based on the type of hazard present.
How are Hazardous Materials Regulated?
Hazardous materials are precisely defined and regulated by government agencies such as the U.S. Occupational Safety and Health Administration (OSHA) and the U.S. Department of Transportation (DOT).
A prominent example of regulation is OSHA’s Hazard Communication Standard (HCS) which requires chemical manufacturers and importers to prepare labels and Safety Data Sheets (SDS) to communicate hazard information to customers. The HCS also requires workplaces to share these labels and SDSs with workers, and to provide proper training in relation to each chemical.
Another example of regulation, the DOT regulates the transportation (across all modes: air, highway, rail and water) of hazardous materials through Title 49 of the Code of Federal Regulations (49 CFR).
These regulations – HCS, SDS, 49 CFR – are at the forefront of chemical logistics requirements. They are also enforceable laws, which means that violations can result in fines and other serious penalties. The right chemical logistics partner will be intimately familiar with all relevant regulations to ensure you are 100% compliant.
Do states like California have additional regulations?
Businesses that store hazardous materials in California are required to obtain a permit from the local fire department or other regulatory agency. Such permitting is very difficult to obtain in major metropolitan areas like Los Angeles, though a few 3PL providers like Weber Logistics do have all necessary permits and have performed hazmat warehousing within Los Angeles safely for decades.
The California Health and Safety Code requires businesses to submit a Hazardous Materials Business Plan (HMBP) to the local fire department if they store certain types of hazardous materials in quantities above certain thresholds.
Additional resources on hazmat warehousing laws and regulations in California include the following.
- California Department of Toxic Substances Control (DTSC)
- California Office of Emergency Services (OES)
- California Fire Marshal's Office
Can any Warehousing Operation Handle Hazardous Material Storage?
No. A warehouse – such as that operated by a third-party logistics provider (3PL) – must be certified to handle hazardous materials. The certification process is rigorous and, as with California, can involve many different government agencies. Each individual process may require lengthy applications, followed by phone and in-person meetings, and in some cases, background checks of key management personnel.
The bureaucracy is thick, but it’s necessary to ensure a safe environment. Since 9/11, security and safety requirements have become strict and unyielding. Regular inspections and unannounced audits can occur at any time.
Can Different Hazardous Materials be Stored Together?
Yes. As discussed in our hazmat chemical storage article, different chemical classes can be stored in the same warehouse but must be stored independently of one another in clearly-marked, segregated areas. Such separation requirements are sometimes necessary for chemicals within the same chemical class. Examples of this include nitric and perchloric acids, which must be kept separate from organic acids like acetic acid.
How is a Hazmat Warehouse different from other warehouses?
Wall composition, diking to contain liquid spills, advanced fire suppression systems and automated doors, atmospheric controls for temperature and humidity, and a host of other factors are parts of the substantial investment in building and maintaining
Can Hazardous Materials be Stored with Non-Hazardous Materials?
Yes. As with storing different types of chemicals in the same warehouse, hazmat materials can be stored in the same facility as non-hazmat materials – provided that the specific storage environments exist in that warehouse, relevant SDS hazard requirements are fully adhered to, and separation requirements are met.
What is CFATS?
Enacted in 2007, the Department of Homeland Security’s (DHS) Chemical Facility Anti-Terrorism Standards (CFATS) identifies chemical facilities that constitute the greatest security risk. Chemical storage facilities that are CFATS-compliant adhere to a set of risk-based performance standards (RBPS) to ensure the safety of their operation.
As each facility is unique, compliance standards are tailor-made by the DHS to suit each of the risk factors present at a given facility.
What Should I Look for in a Hazardous Material Storage Provider?
The liability and safety risks associated with hazardous material storage and shipping demand a careful evaluation of 3PLs and/or other chemical logistics service providers. This evaluation should include a close look into the provider’s reputation, the background and experience of key personnel, industry certifications (e.g., the NACD), and analysis of the transportation that is likely to be involved (with chemicals, fewer miles are better).
For a comprehensive guide to evaluating a provider, read the free Weber Insight: What You Need to Know About Chemical Warehousing.
Hazmat Storage Specialists
When storing chemicals and hazardous materials, you generally have two options. You can invest the time, resources, and money to build a facility – or upgrade an existing one – so that it can handle hazmat and comply with regulations, or you can partner with a hazmat storage specialist that has already done that work for you. Such companies have made the necessary investments to upfit their facilities and are ready to handle your products from Day 1.
As an example, Weber Logistics’ chemical storage operation in Santa Fe Springs, CA includes:
- 13 segregated rooms to handle specific product types and temperature ranges.
- Segregated H2, H3, H7 and S2 occupancy areas.
- Safety features, such as EE-rated equipment and firewalls.
- Corrosive Room, oxidizer rooms, temperature-controlled flammable storage and heated rooms (75° - 90°).
- A team of on-site hazmat specialists that assume responsibility for training, DOT compliance, SARA reporting, SDS training and reporting, and compliance with NFPA, UFC, IATA and OSHA standards.
Many of the same features can also be found at Weber’s Chino, CA chemical storage warehouse, including:
- Warehousing and distribution of flammables, corrosives, aerosols, oxidizers, and non-hazardous industrial products
- Ambient, chilled, freezer, flammables, corrosives, aerosols, oxidizers, industrial non-hazmat storage zones
- Segregated H2, H3 occupancy areas.
- Safety features such as EE-rated equipment and firewalls.
- A team of on-site hazmat specialists that assume responsibility for training, DOT compliance, SARA reporting, SDS training and reporting, and compliance with NFPA, UFC, IATA and OSHA standards.
Turn to Weber Logistics for Hazardous Material Storage
At Weber, chemical logistics has been a company focus for over 50 years. We understand the operational and regulatory requirements for handling a range of chemicals. In fact, Weber’s chemical handling processes are a model for the Los Angeles County Fire Department’s Training Program.
This expertise allows us to create the safest environment for our staff and your product. To learn more about our chemical logistics services, contact Weber today.