Recent, Happening Now
July 16, 2025
WEST COAST AND CALIFORNIA LOGISTICS BLOG
Subscribe to instant updates library group background effect move style move subtract object pencil fill invite.
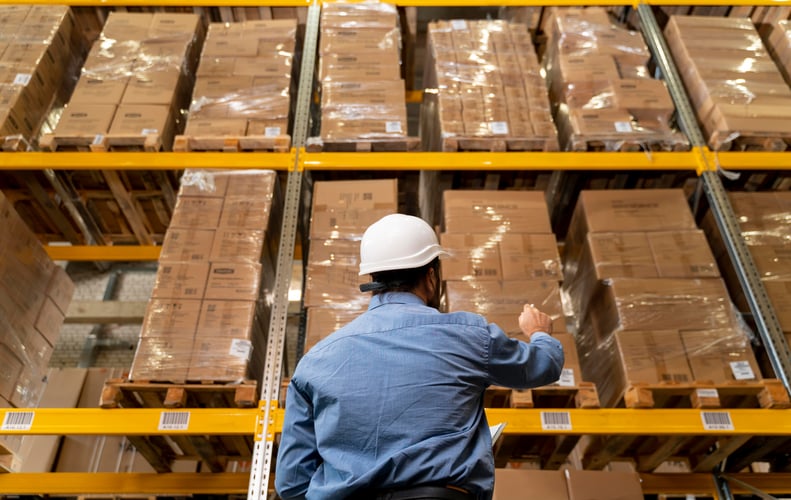
FILTER BY TOPIC
Recent Blog Posts
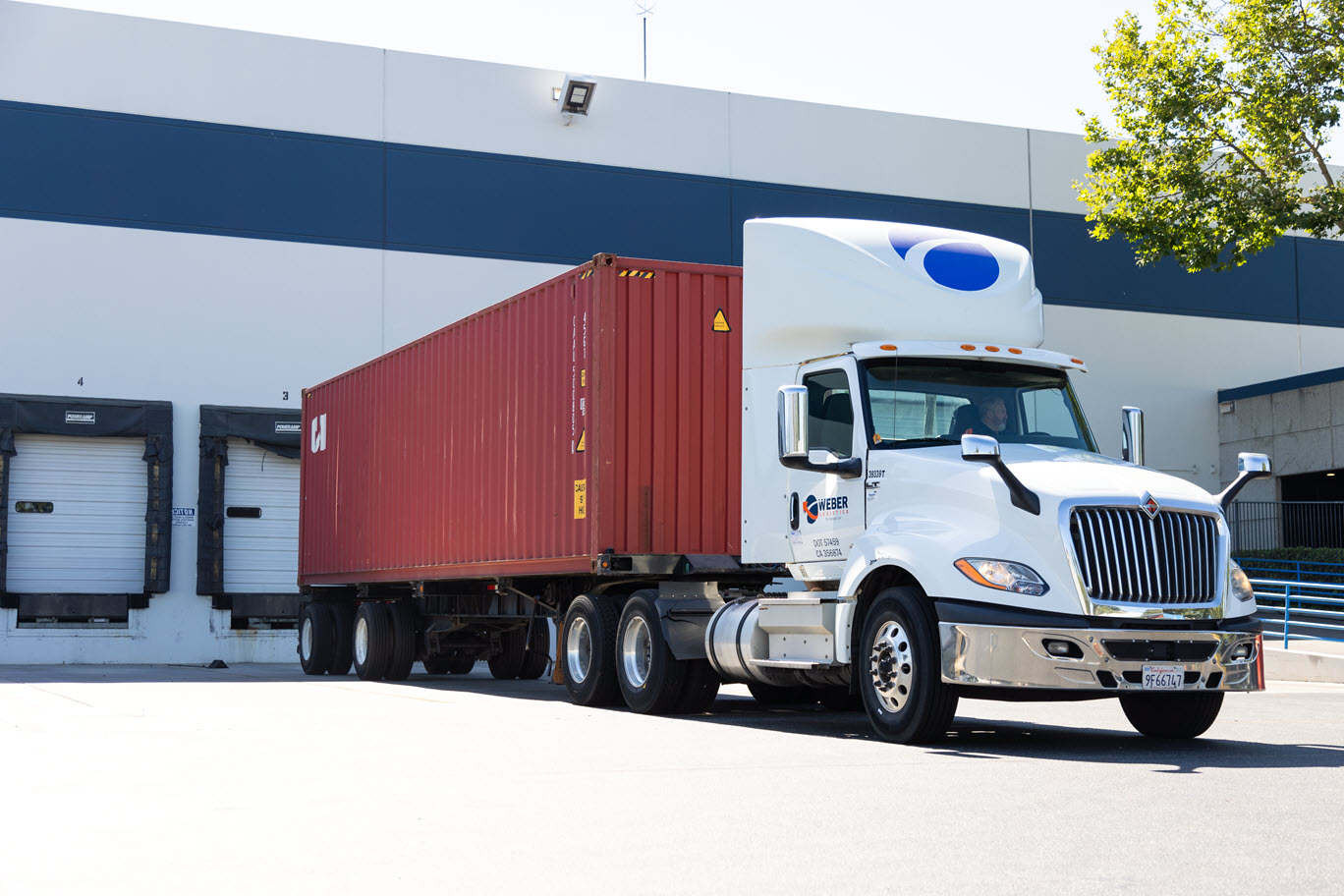
Recent, Happening Now
July 14, 2025
What Drayage Looks Like with an Integrated Cold Chain 3PL
In today’s world of temperature-sensitive logistics, food and beverage brands face a dramatically evolving playing field. New regulatory demands, heightened customer expectations, and razor-thin...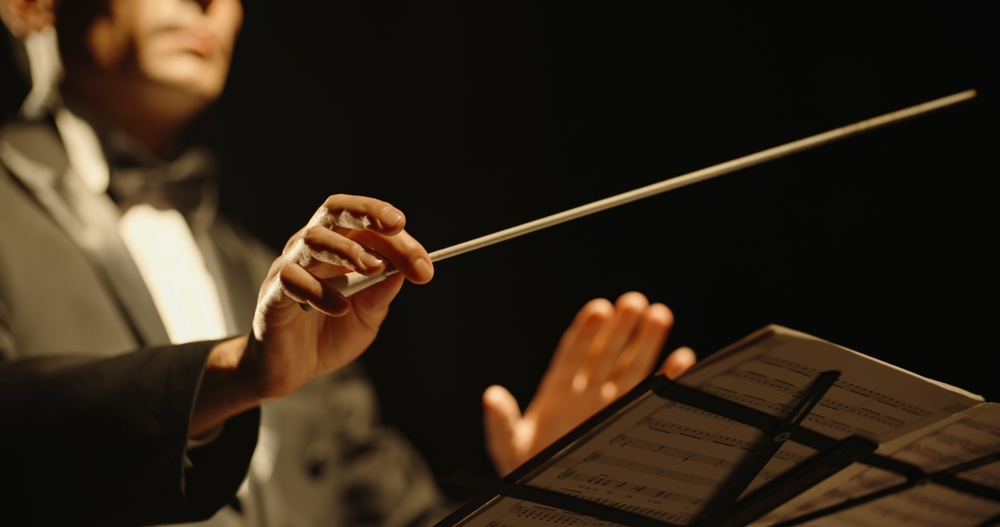
Recent, Happening Now
July 1, 2025
Why Work with an integrated Cold Chain 3PL Provider
Refrigerated freight doesn’t move itself. It takes people, systems, and tightly coordinated processes to keep food and confectionery products safe, compliant, and on schedule. Yet in today’s...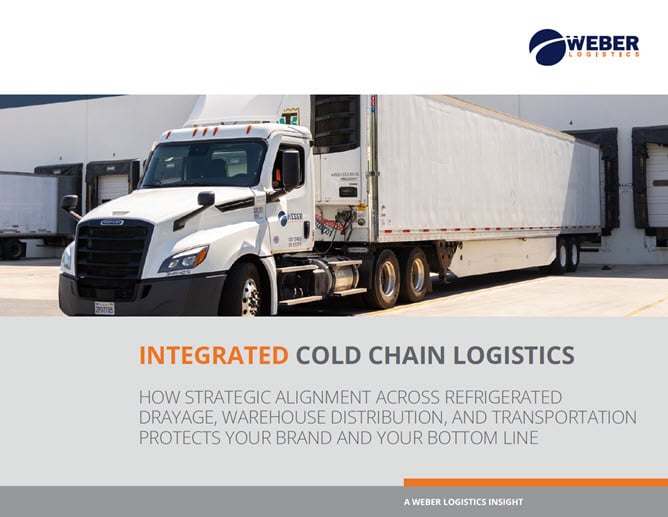
Recent, Happening Now
June 19, 2025
New eBook: Rely on an Integrated 3PL to Orchestrate Your Cold Chain
In today’s fast-paced supply chain environment, maintaining product integrity from origin to delivery has never been more critical—especially when it involves temperature-sensitive goods like food...All Blog Posts
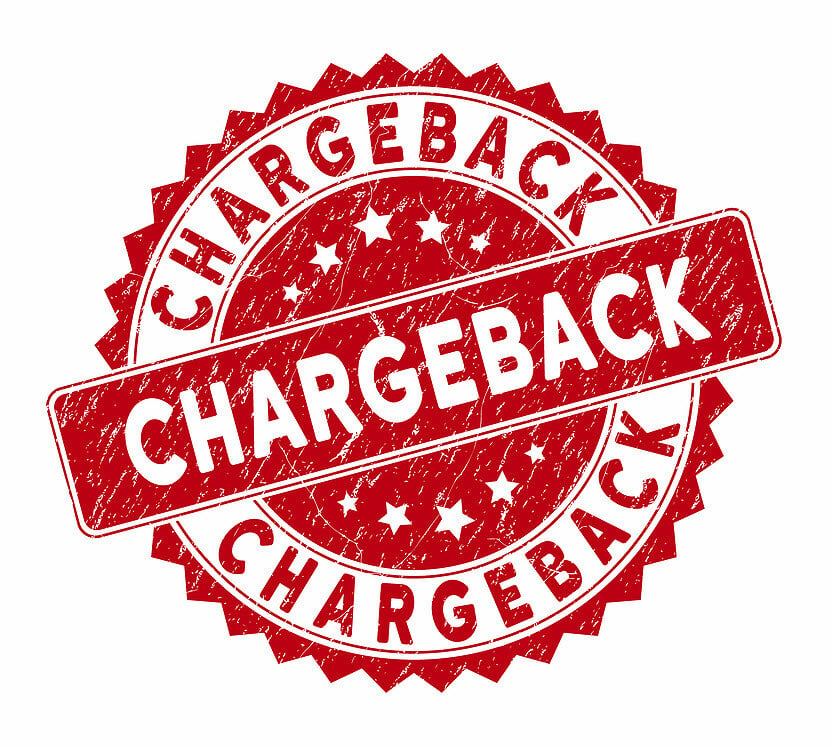
Chargebacks
February 27, 2025
How Retail Chargebacks Work and What You Can Do About Them
All major retailers issue chargeback penalties for non-compliant shipments from their suppliers. The specific penalties are explicitly laid out in each retailer’s routing guide and range from about...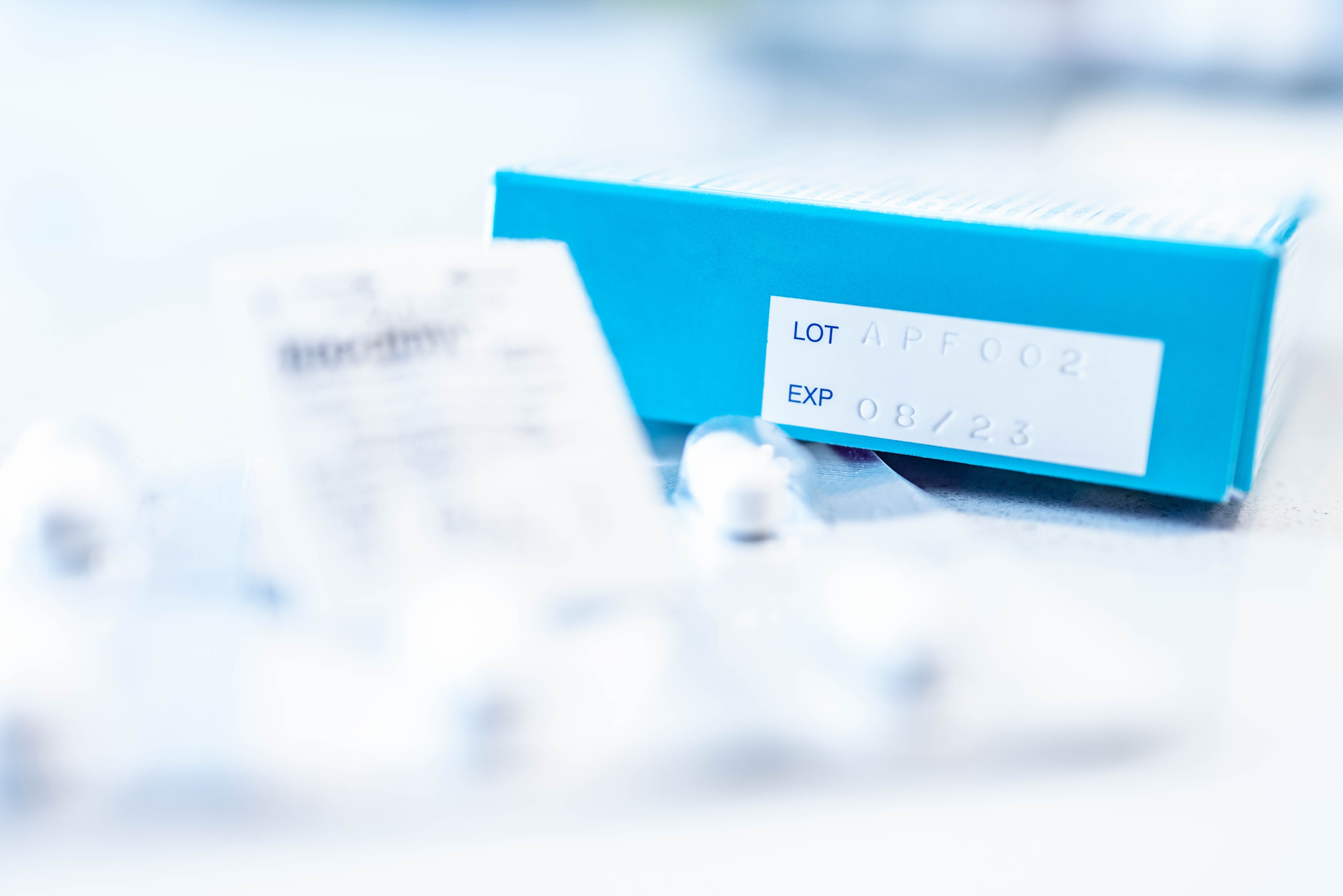
Pharmaceutical Logistics
December 11, 2024
What to Look for in a Pharmaceutical Logistics Provider
Pharmaceutical logistics is a highly specialized field that requires precision, compliance, and a deep understanding of the unique demands of this tightly regulated industry. Selecting the right...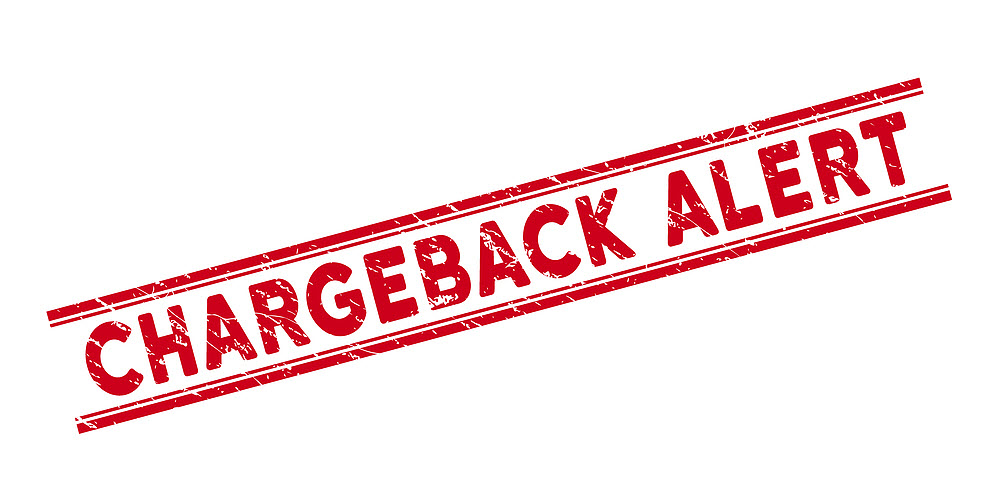
Vendor Compliance
November 9, 2020
Retail Compliance Requirements: Common Chargebacks
Retail compliance requirements are more numerous than ever these days, creating challenges for retail vendors as they try to meet routing guide demands and avoid chargebacks. These chargebacks –...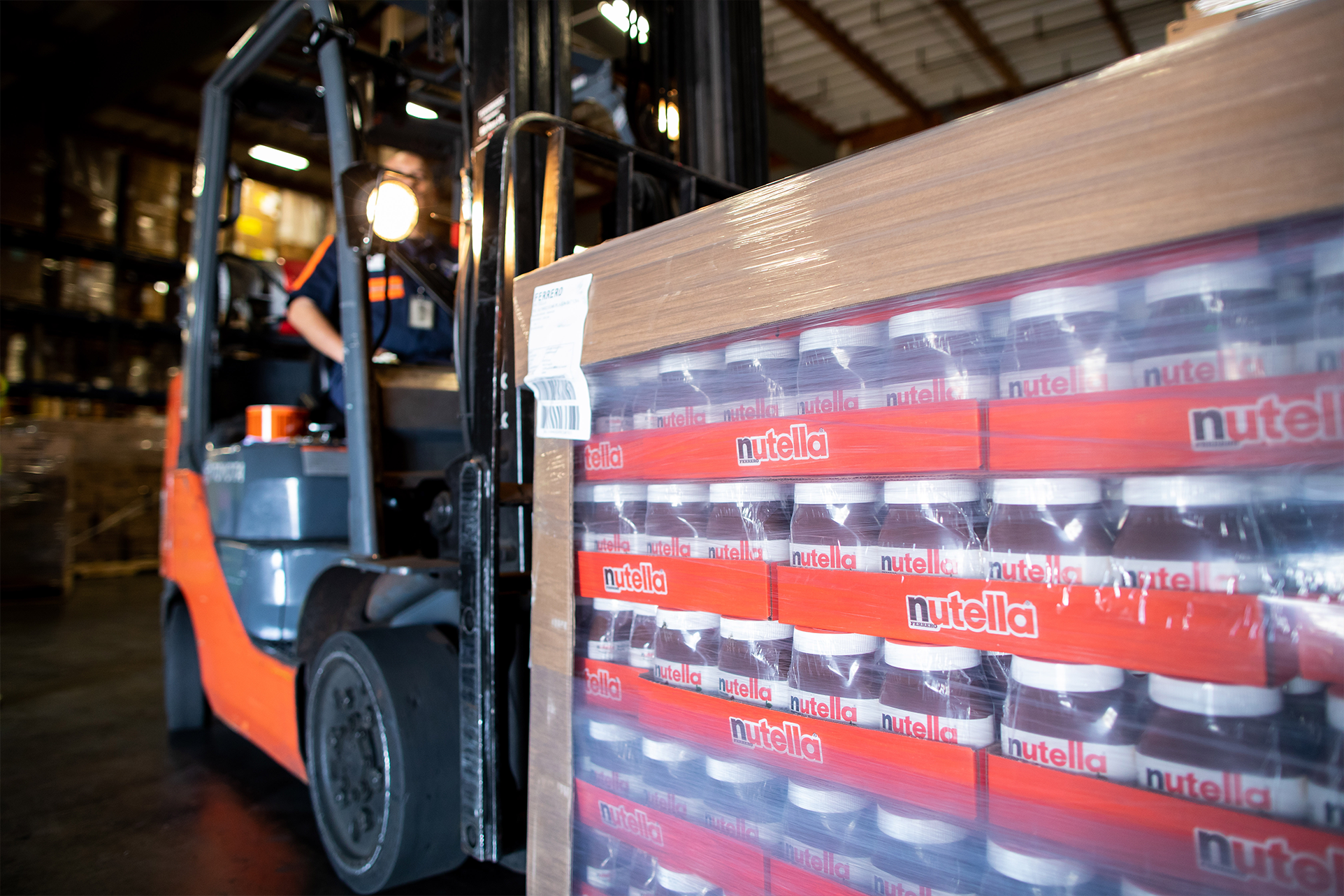
Public Warehousing
April 25, 2019
5 Things to Look for in a Food Warehousing Provider
When you entrust your food and confectionery products to a food warehousing provider, you’re relying on that company to be much more than a provider of space. You’re really relying on them to be a...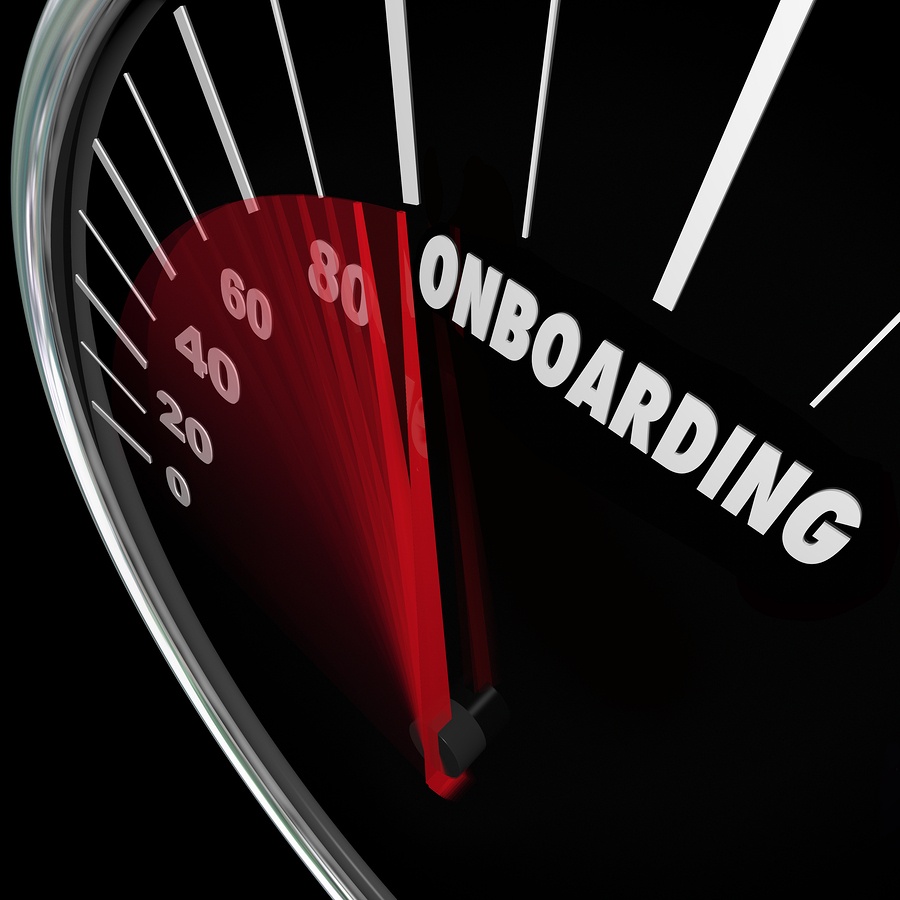
Vendor Compliance
April 27, 2018
3PL Onboarding and Retail Compliance Requirements
Whether it’s your first time outsourcing or you’re changing providers, partnering with a new third-party logistics (3PL) provider is an exciting time for your logistics operation. It is a time for...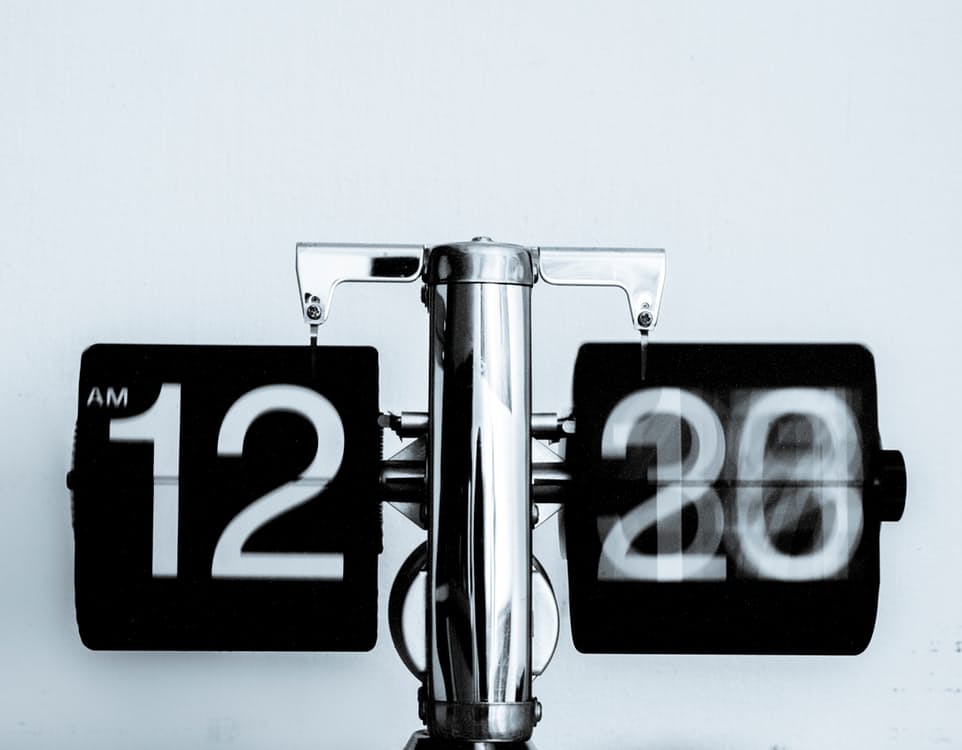
3PL
January 6, 2017
A Spotlight on KPI Metrics: On-Time Shipping
Holding your 3PL accountable to deliver on the service promise can be difficult. However, a key component of that is monitoring key performance indicators (KPI’s).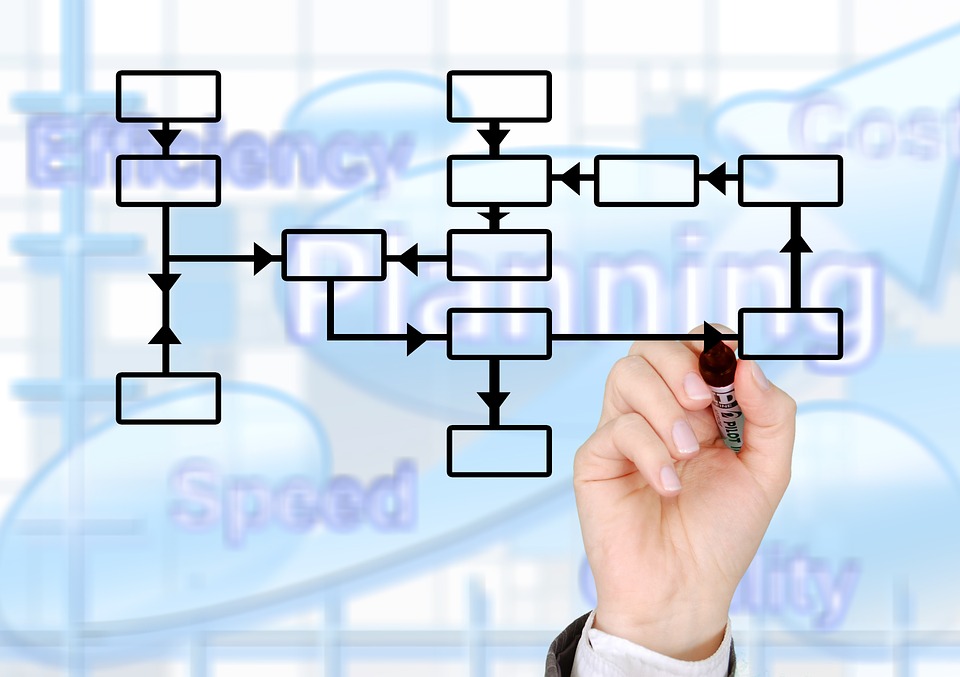
Logistics Management
August 23, 2016
The Key to Upholding Quality in an Operation: Internal Audit Programs
Does your warehouse or 3PL provider have an internal audit program in place? It is critical for all operations follow standard operating procedures (SOP’s) – that’s how you get to the quality we need...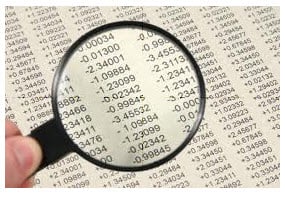
Warehouse Rates
January 22, 2014
Review Your Warehouse Technology to Reduce Chargebacks
It’s a new year, and with it comes a new cycle for chargeback deductions. Hopefully, if previous errors do not reoccur and the wrongs have been righted, then vendors stand a better chance of warding...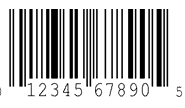
Warehouse operations
June 24, 2013
What are barcodes and how do they work in fulfillment warehouses?
(Mimi Ma is Director of Quality and Compliance at Weber Logistics)Subscribe to Instant Updates
Component variant main layer object list link mask create follower main vertical image blur comment bold variant opacity plugin italic.
