Recent, Happening Now
August 26, 2025
WEST COAST AND CALIFORNIA LOGISTICS BLOG
Subscribe to instant updates library group background effect move style move subtract object pencil fill invite.
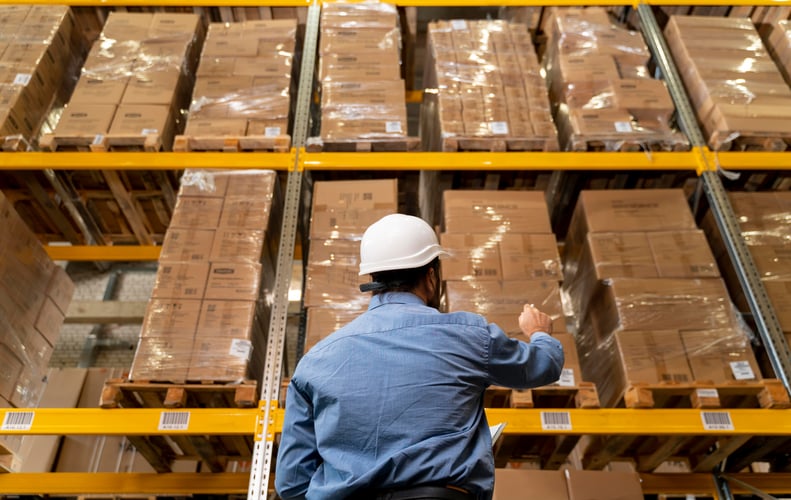
FILTER BY TOPIC
Recent Blog Posts
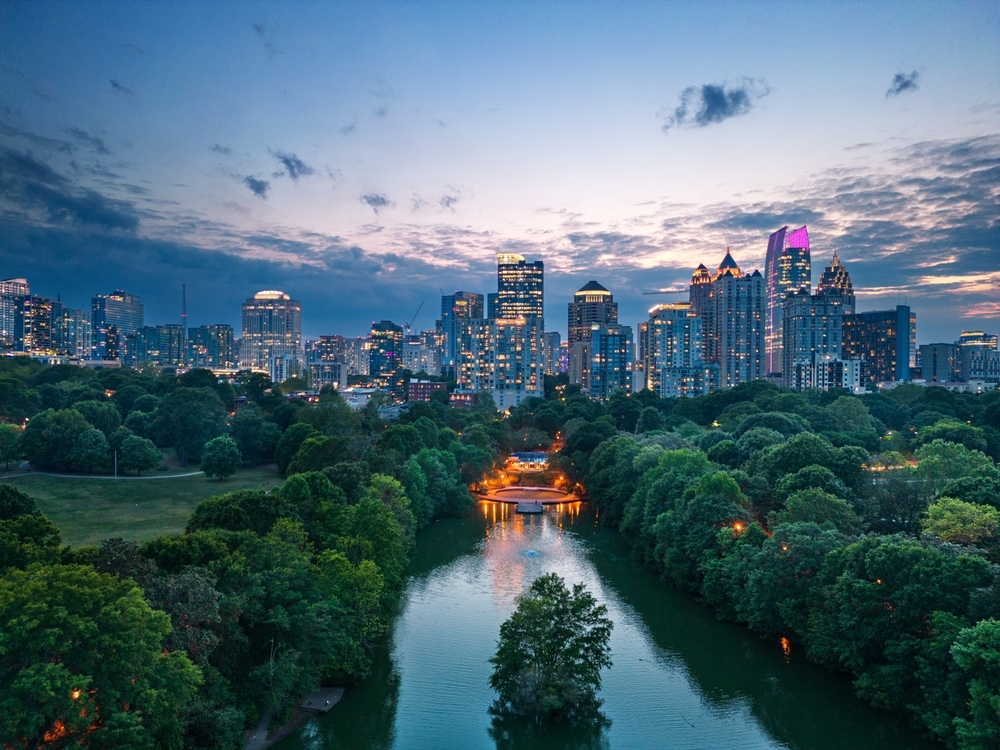
Recent, Happening Now
August 21, 2025
The Advantages of Using Atlanta as a Logistics Hub
The state of Georgia consistently ranks at or near the top of ‘best states for business’ lists in publications like Area Development and Site Selection Magazine. It’s no surprise, then, that Weber...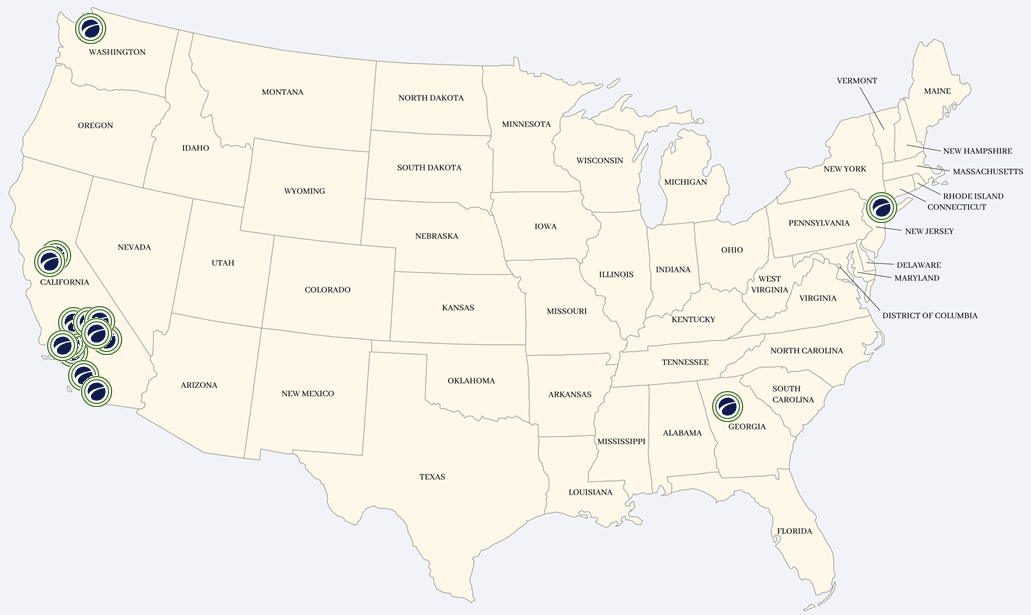
Recent, Happening Now
August 18, 2025
Weber Logistics Goes National: Now Serving Atlanta, Seattle, and New Jersey
For over 100 years, Weber Logistics has been a trusted West Coast logistics partner, moving products seamlessly from port to shelf with precision, speed, and care. Now, we’re bringing that same...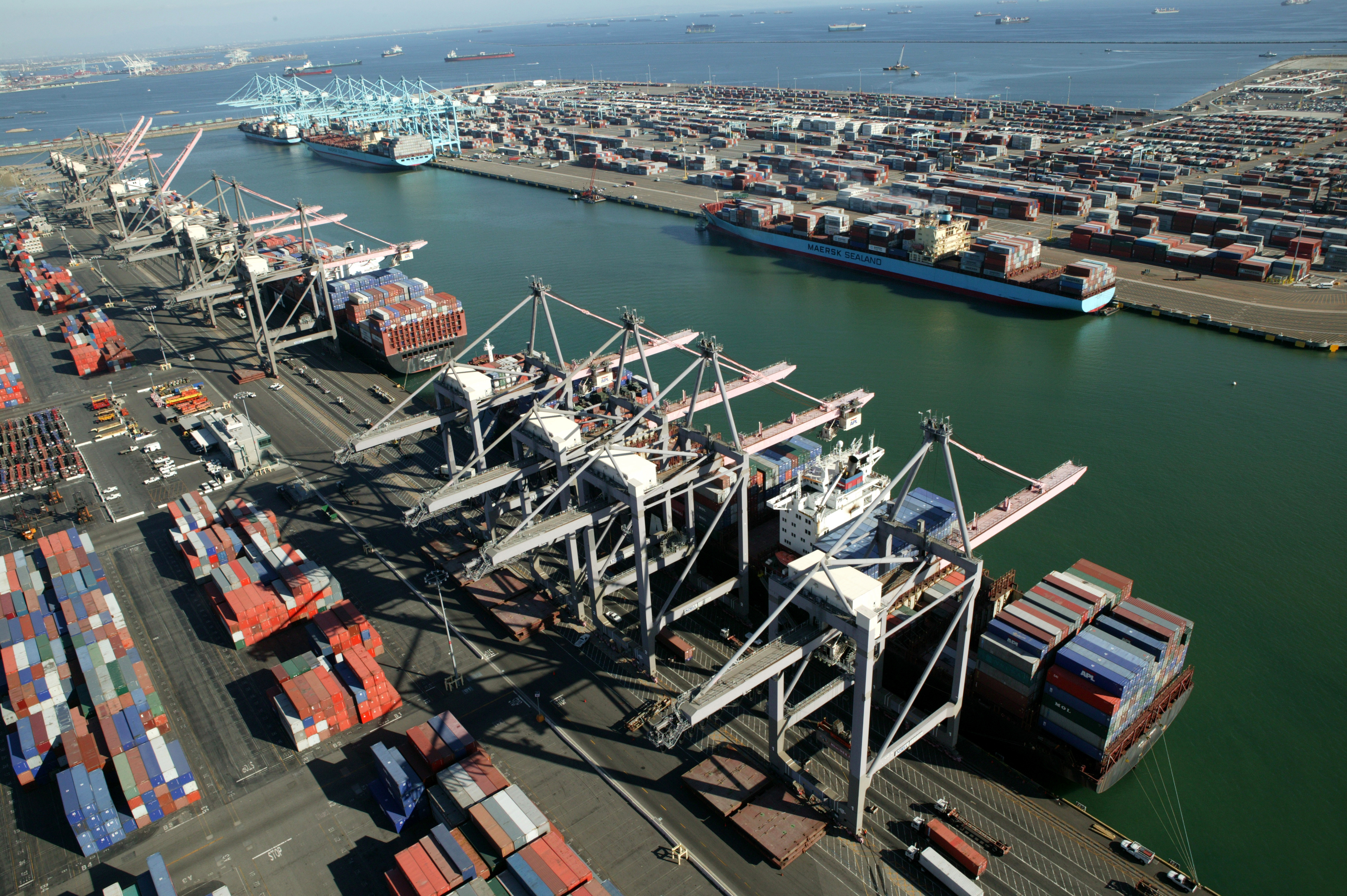
Recent, Happening Now
July 16, 2025
Happening Now: Port of Los Angeles Sees Record June
According to FreightWaves, the Port of Los Angeles had its busiest June on record, moving 892,340 TEUs—an 8% increase year-over-year. This is due, in large part, to retailers accelerating holiday...All Blog Posts
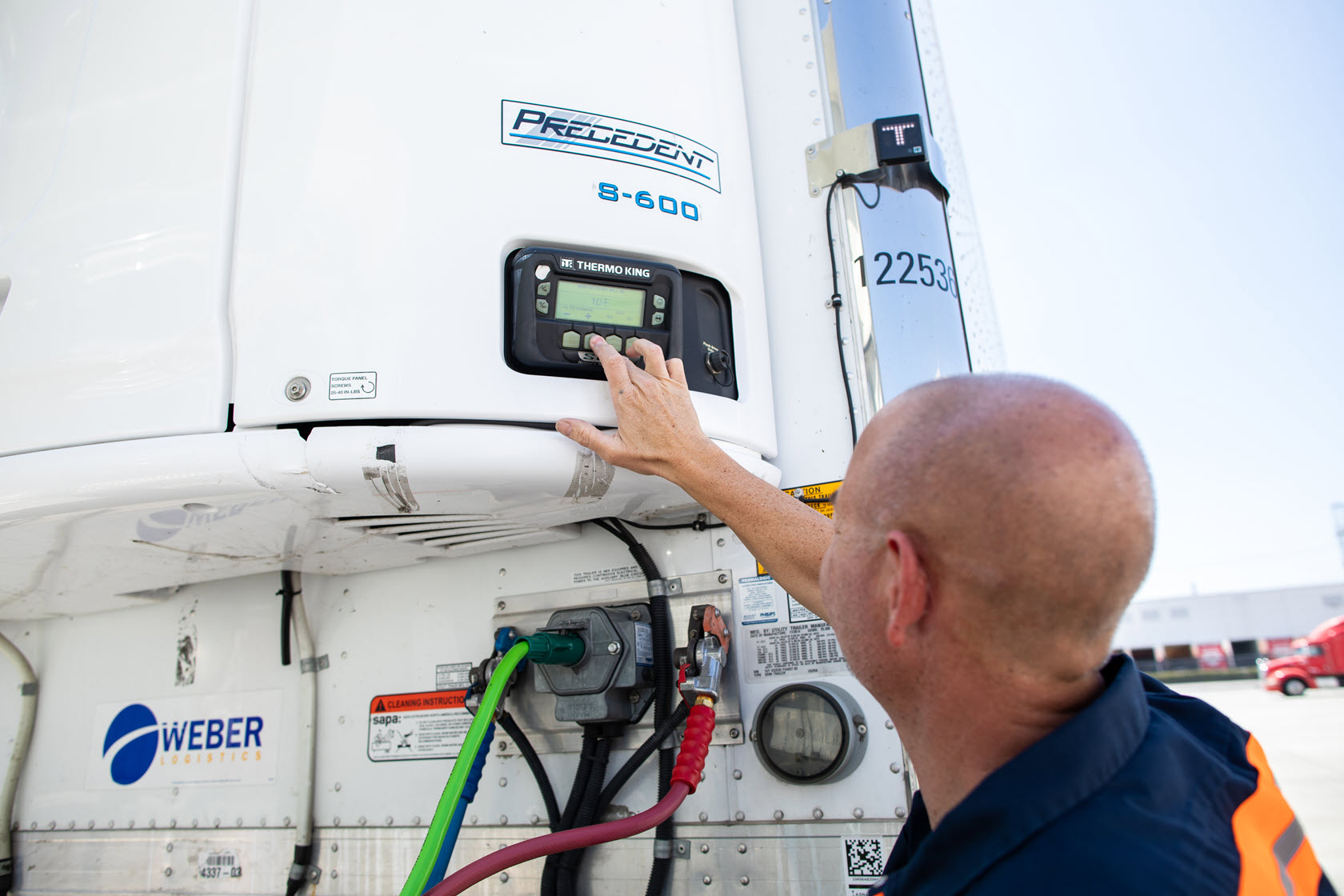
Cold Chain Managment
April 30, 2024
The Guide to Choosing a Temperature-Controlled Transportation Provider
In the intricate world of temperature-controlled trucking, selecting the right provider is the key to ensuring the safety and quality of your products during transit. In this article, we cover 5...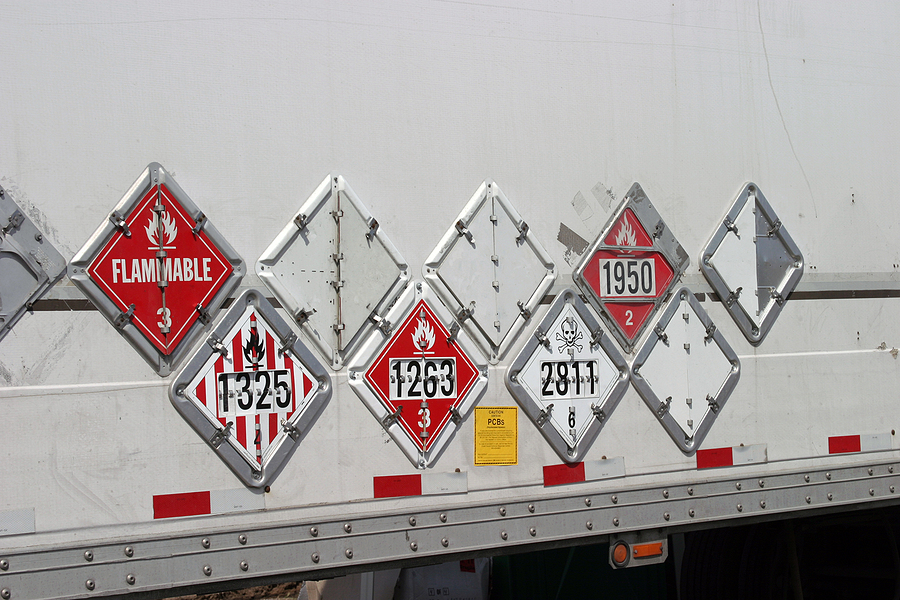
Chemical Logistics
April 18, 2024
A Guide to Safe Chemical Trucking
Hazardous materials barreling down the highway in an 80,000-pound tractor trailer – what can go wrong? Unfortunately, a lot can.
Chemical Logistics
August 27, 2015
The Same Game with Different Rules - Chemical Warehousing
Chemical Warehousing 101 Whether you’ve been in the game for years or have just jumped in, you know when it comes to chemical warehousing, a whole new rule book applies.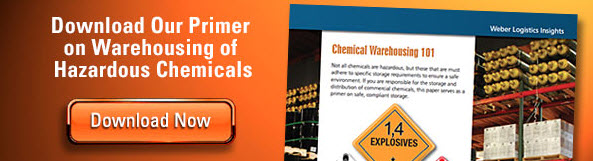
Chemical Logistics
January 21, 2015
Chemical Warehousing 101 – New Primer Available
Chemical Warehousing 101 – New Primer Available The rules of warehouse storage for many product types are quite similar. But when it comes to chemical warehousing, a whole new rule book applies.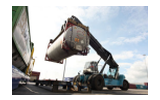
3PL
December 3, 2014
Choosing a Chemical Warehouse Provider
You’re not going to choose just any 3PL to store and ship your chemical products. The liability and safety risks associated with hazmat storage and shipping are just too great. But how can you...Subscribe to Instant Updates
Component variant main layer object list link mask create follower main vertical image blur comment bold variant opacity plugin italic.
