When outsourcing warehouse distribution, it’s essential to find the right 3PL partner. One that understands how to run a food-grade warehouse and remain in compliance with all regulatory requirements.
How do you know which 3PL to trust with your food logistics requirements? Here are five questions every food shipper should ask.
1) Can the 3PL monitor and maintain temperature integrity throughout the supply chain? A 3PL that understands food-grade warehousing will deploy technology to monitor the environment through all phases of the supply chain – in the warehouse, on the dock and on the road. Any time the temperature slips above or below the ideal range, the system sends an alert, and an expert steps in to correct the problem.
2) Can the 3PL meet all your customers’ requirements for code date compliance, FIFO and other picking rules? While all your customers want to maximize product shelf life, each of them has different ideas about how to achieve that goal. Code date, expiration date, best used by date, FIFO, FEFO, LIFO – any of them might apply to a specific customer. Get the details wrong, and you could get stuck with product your customers refuse to take. Look for a 3PL with a sophisticated WMS that supports a broad range of picking methodologies. The 3PL's systems should be able to produce snapshots of remaining shelf life for any products in your warehouse, alert you to product that’s within 30 days of its expiration date, tell you which product has the oldest code dates, and more.
3) Can the 3PL help you reduce supply chain costs? Marketing food products is a low-margin business. To maximize profit, you need to minimize costs, and that means making your food warehouse operation as lean and efficient as possible. Unproductive employees, sub-optimized transportation routes, refrigeration systems that draw too much power – all put further strain on an already low profit margin. The ultimate measure of supply chain efficiency is the cost of moving each case of product to your customer. Your 3PL should demonstrate how it keeps that per-case cost as low as possible with smooth, efficient warehousing and transportation services.
4) Can the 3PL meet government requirements for tracing food shipments? From the FDA to the USDA to the SEC, federal agencies have enacted a mass of regulations that describe how vendors of food for humans and pets must perform during a product recall. Even if nothing ever goes wrong with your product, you must be able to prove that you can track and trace any item by lot number. Companies that don’t meet government mandates can suffer significant penalties. A sophisticated WMS provides the capabilities a 3PL needs to trace products once they leave the warehouse. The 3PL should have written SOPs for performing a recall, and it should conduct mock recalls periodically, not only when a customer asks for one.
5) Does the 3PL have plenty of solid experience handling food-grade products? Any 3PL can claim to have experience with food-grade products, but how many transactions has the company handled, and for how many years? How many satisfied customers does it serve in the food industry? How many different kinds of food has it managed? Inexperience comes with a cost.
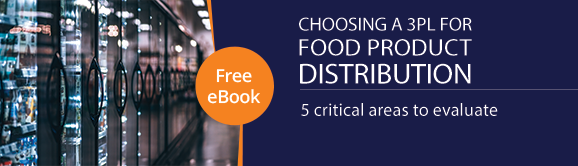